Application:
Rotary screen is designed to separate coarse mechanic impurities
from liquid. It is used rather conveniently as first stage of
mechanic pretreating (preliminary clarification) within municipal
or industrial waste water treatment plants (CPI - Corrugated
Plate Interceptor) and anywhere where solid phase is required
to become separated from the liquid one with minimal solid particle
size of 5 mm.
Function Description:
A liquid containing solid materials flows due to the gravity
into the rotary screen via a supply nozzle (neck). While being
treated the liquid flows over the screen perforation complete
with undissolved materials (herein UMs only) smaller than 5
mm. UMs separated by means of the screen are then raked in a
controlled manner by means of the raking arms, and pass right
into the hopper of the hydraulic press’ operating chamber. Once
inside the operating chamber the rackings get dewatered, pressed and sent
to the container via conveyance piping.

|
Specifications:
Rotary screen is electric motor-driven using hydrostatic
transmission. Motor power output installed equals to 0,37
kW. Hydro unit’s operating pressure is 16 MPa. There is
fully automatic control with independent time adjustments
for raking and pressing of rackings. There is either left-side
or right-side supply of water to the rotary screen as
required. Standard connection to the drainline uses sewer
coupling of respective opening. If required flange connection
or any other method are suitable to be made. Conveyance
piping with pressed rackings is led at 45° or 90° angles.
Maximal conveyance height of pressed rackings is 5 m (overhead
the supply line axis). |
|
Material Version:
Rotary screen is made of 17241 class steel. Hydraulic unit
is made of normal structural steel with surface finish using
synthetic paint. Electric switchboard is of plastic version.
Supply Specification:
The supply comprises rotary screen complete with hydraulic
press designed for rackings, electric switchboard, control system
and conveyance piping for rackings and terminated with flange
DN 200, PN 6 of total length equal to 200 mm overhead D1 diameter.
The basic version provides for anchoring rotary screen by means
of frame to the supporting structure with anchore bolts spacing
A x B. If required, please specify beforehand any other requirements
concerning the anchoring and connection to the influent conduit.
HYDRAULIC PARAMETERS:
TYPE |
O Influent
Conduit |
O
Screen Perforation |
Maximal Flowrate |
DN (mm) |
(mm) |
Q (l/s) |
RSX 300 |
150 |
|
9 |
200 |
|
1 |
RSX 400 |
300 |
5, 6, 8,
10 |
35 |
400 |
50 |
RSX 500 |
500 |
|
80 |
600 |
|
100 |
ROTARY SCREEN SKETCH:
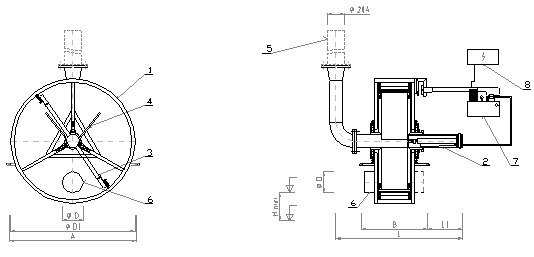
Download: AutoCAD_01
Legend:
1 - Screen Supporting Frame
2 - Hydraulic Press Operating Chamber
3 - Raking arms
4 - Hydraulic Press Hopper
5 - Conveyance Piping for Pressed Rackings
6 - Influent Nozzle
7 - Hydraulic Unit
8 - Electric Switchboard
Construction and Anchoring Dimensions:
TYPE |
Fixing Dimensions
|
Construction
Dimensions |
A |
B |
L |
L1 |
D1 |
Hmin |
(mm) |
(mm) |
(mm) |
(mm) |
(mm) |
(mm) |
RS 300 |
1500 |
782 |
1350 |
570 |
1480 |
100 |
RS 400 |
1600 |
882 |
1750 |
715 |
1580 |
150 |
RS 500 |
1700 |
982 |
2050 |
900 |
1680 |
200 |
Terms:
Offer developed within 2 - 3 days. Equipment deliveries within
ca 3 months.
Warranty and Service:
The equipment warranty is 24 months. After-guarantee service
performance is expected within two weeks after receipt of
such order.
Advantage:
- Separation of undissolved materials along with their pressing
and conveying are contained within one single unit.
- By pressing the rackings you minimalize their quantity
and you constrain their odour to generate and propagate
when water evaporates from non-compressed rackings and their
decaying.
- Install your equipment right within the refill stations
to enable for not installing disintegration pump that has
higher electric power consumption, but instead use normal
sludge pump.
- Hydrostatic transmission protects electric drive motor
in a very efficient way against any damage caused by its
overload.
- If required, the equipment can be fitted with the waterproof
bottom and outfluent conduit full of pretreated water. Thus
no precondition exists to carry out mechanic pretreatment
with no need to build concrete channel, e.g. right within
the screw pump discharge.
- Material version along with simple and robust stainless
steel structure ensures high lifetime.
The hydraulic drive chosen provides for incomparably lower
demands in terms of maintenance, services and operation,
when compared with drive rotary systems.
Other examples of RSX rotary screen
installations: |
|
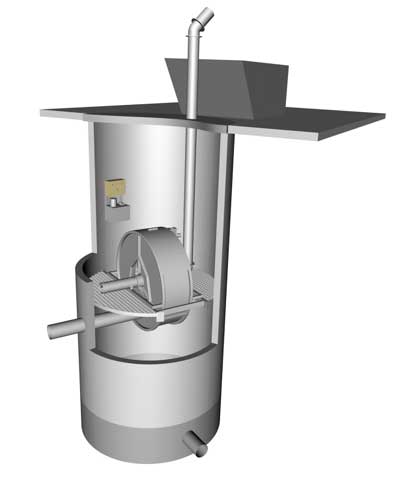 |
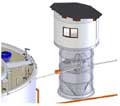 |
|